Gekko Systems is a global leader in mineral processing, providing fully integrated solutions to mining companies around the world. We discuss new investments and working ‘smarter together’ with General Manager of Global Sales and Solutions, Nigel Grigg.
THE GOLDEN PROSPECT
The Gekko Systems (Gekko) company manifesto reads, “only by embracing smart ideas together can we transform our world.”
Summarising this belief in the company tagline “smarter together”, it seems obvious that to achieve meaningful change, and to transform mining and the environment, the entire industry must collaborate. Gekko endeavours to spearhead this evolution and to deliver step-change benefits, on a global scale, through innovative mining solutions.
Having studied metallurgy at the University of Ballarat, Gekko’s General Manager of Global Sales and Solutions, Nigel Grigg had always wanted to be involved in the mining industry, as it entailed lots of opportunities to travel, both domestically and internationally.
“Directly after graduating, I was fortunate enough to assist a Canadian company to develop a small mine in Ballarat,” he begins.
“The gold in Ballarat is very coarse, and so it was challenging with the basic Carbon In Leach circuit (CIL) we had to get good gold recoveries. I introduced a gravity circuit into the circuit using an InLine Pressure Jig (IPJ) from Gekko and the recoveries dramatically improved.
“I was very impressed with the technology and the business, so when the Ballarat mine closed due to the low price of gold at the time, I asked the two founders Sandy Gray and Elizabeth Lewis-Gray if I could join them, and the rest is history.”
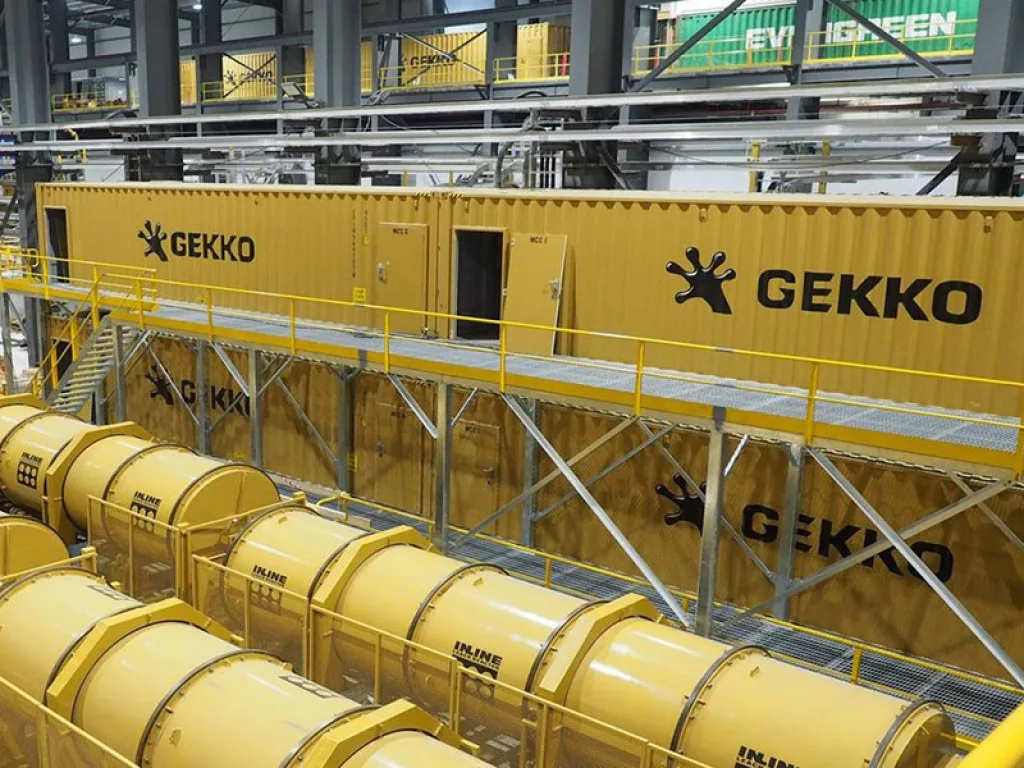
Solutions and Growth
Having opened offices in South Africa, Brazil, Canada, Australia and Russia over the past 26 years, Gekko has developed strong capabilities in the design, manufacturing, installation and commissioning of energy-efficient mineral processing equipment and completes plants for a wide range of minerals including gold, silver and polymetallics.
One of Gekko’s main products is the InLine Leach Reactor (ILR). Gekko’s user-friendly ILR offers superior recoveries in a proven, high-efficiency, safe and highly secure system. The ILR’s innovative design and unparalleled flexibility in gold and silver leaching chemistry provides cost and production benefits to operations across more than 40 countries around the globe.
The ILR is available as a completely automated batch model for processing high grade gravity gold concentrates. Uniquely, the unit can also be configured as a continuous model for treating high-throughput gold, silver and complex sulphide concentrates from IPJs and flotation circuits.
The IPJ is another one of Gekko’s signature products. The efficient circular IPJ design delivers 20 percent less power and consumes only 10 percent of the water required by traditional jigs. Furthermore, the low separating velocity within the unit maximises the recovery of fine mineral particles. Saving water and reducing energy helps mine operations lower their environmental impact and remain profitable. The IPJ is being used in several pre-concentration applications recovering several different minerals.
Gekko also designs and builds modular plants for given mine operations with specific requirements. The innovative core technologies and in-house process design expertise continue to produce agile and effective modular plants.
Innovation and collaboration have been integral to Gekko’s growth, not only with the products that the company has developed but also with the internal process that is followed within the organisation. As a highly vertically integrated company, Gekko performs a number of tasks such as testing, engineering, designing, manufacturing and installing, covering a wide range of disciplines within the company.
Gekko also offers on-site performance consulting services for customers looking to optimise established process plants and achieve the highest operational performance. Its range of solutions offers value for remote and environmentally sensitive operations with high energy costs.
“Gekko uses a flexible work model with 70 to 120 staff members depending on the projects that we might be working on at the time,” Grigg tells us.
Gekko differentiates itself within the mining sector by having a genuine interest in making a significant difference in the industry. The company prides itself on investing in the R&D side of the business and viewing problems from a different perspective.
The company also invests a considerable amount of time and resources into its staff to become agents of change and has a very nimble approach to solving problems within the mineral processing field.
“As well as our investment in people, we have a very strong focus on modular solutions, and are always looking at how to remove energy from our flowsheets in order to optimise the operating costs and lower life-of-mine capital costs,” expands Grigg.
Focusing on removing energy from the company flowsheet not only reduces the obvious issue of operating costs, but also helps Gekko and its clients towards the aim of being carbon neutral by 2030. Climate goals remain very topical at the moment, and Gekko is doing as much work as it can to remove the power required in its equipment and still achieve economic recoveries.
“We spend a lot of time looking at the liberation size of the minerals in order to determine the coarsest possible size that can achieve good recoveries, in turn helping reduce crushing and grinding costs from the flow sheets,” he says.
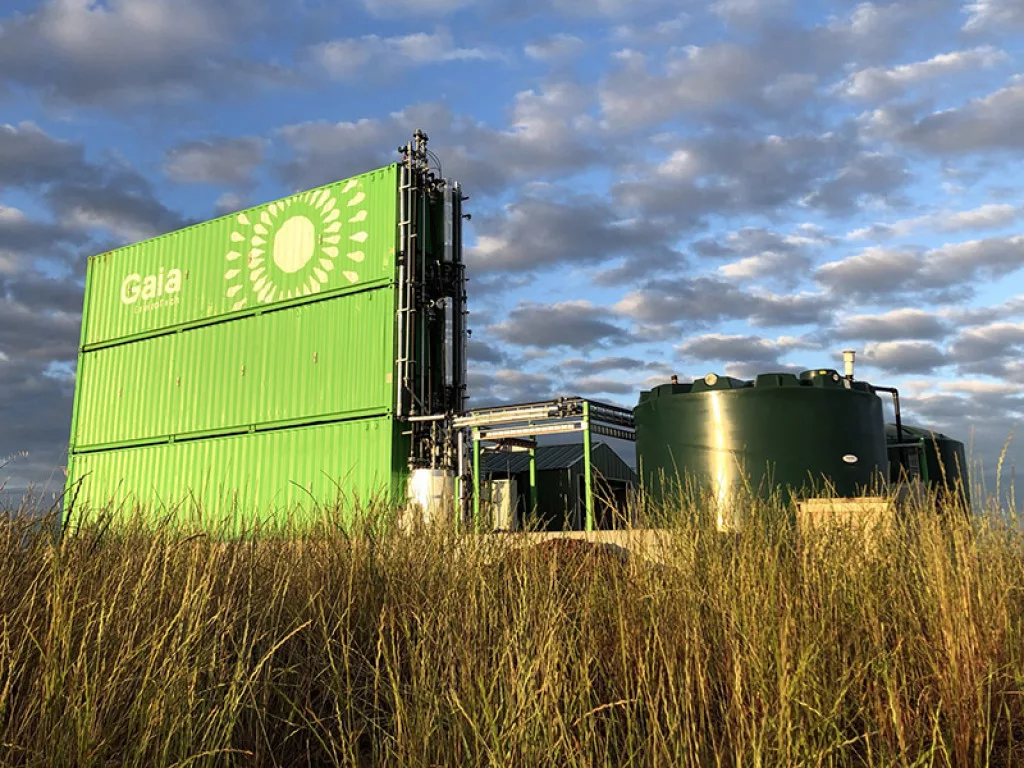
‘Only by embracing smart ideas together can we transform our world’
Gekko Systems
Innovative new products
The Carbon Scout is one of Gekko’s newer products that was developed in collaboration with the Curtin University in Western Australia (WA). The unit enables the plant operator to automatically get the carbon inventories, pH and density measurements from a single ground-based unit. This then automates the carbon transfers into each tank, ensuring that the gold solution losses are kept to a minimum. This can potentially result in thousands of dollars’ worth of extra gold being recovered by simply optimising the carbon concentrations in each of the CIL tanks.
“More recently, we have also installed an XRF sensor to determine the gold on carbon levels and as a result, we can now automatically calculate gold in circuit measurements,” details Grigg.
These would normally be calculated manually using samples and assay data that could often take a few days to obtain. Instead, the Carbon Scout allows for these calculations to be taken every few hours. This is important for mine owners to know how much gold is in the circuit at any particular time, and can also assist the operators to determine when stripping and carbon movements are required.
“So far, we have over 10 units operating internationally, and they are providing great benefits to our clients,” he acclaims.
Located near the town of Grassy on the coast of King Island, Tasmania, Gekko has engaged with Group 6 Metals (G6M) to design, manufacture and construct the processing plant for the King Island Dolphin Project. Gekko has traditionally been very focused on the gravity gold market, and the processing flowsheet for Scheelite utilises several gravity recovery process steps; it was therefore the perfect fit for Gekko to utilise its previous experience and move into the critical mineral space.
“The flowsheet was developed by G6M in conjunction with ourselves to design a circuit that was able to recover the Scheelite at the optimum liberation size,” Grigg explains.
Gekko has been able to supply key liberation equipment including bespoke milling and VSI modules to ensure that the brittle Scheelite mineral is not overground and is liberated for optimum gravity recovery. The company will now be involved in commissioning and ramping up the project for G6M, ensuring that it can start up as efficiently as possible.
Grigg tells us how Gekko believes that its “focus on liberation and gravity recovery at the coarsest possible size will be a key factor in reducing energy within the process flowsheet, and will be important as the critical mineral industry continues to be a key focus in the global market.”
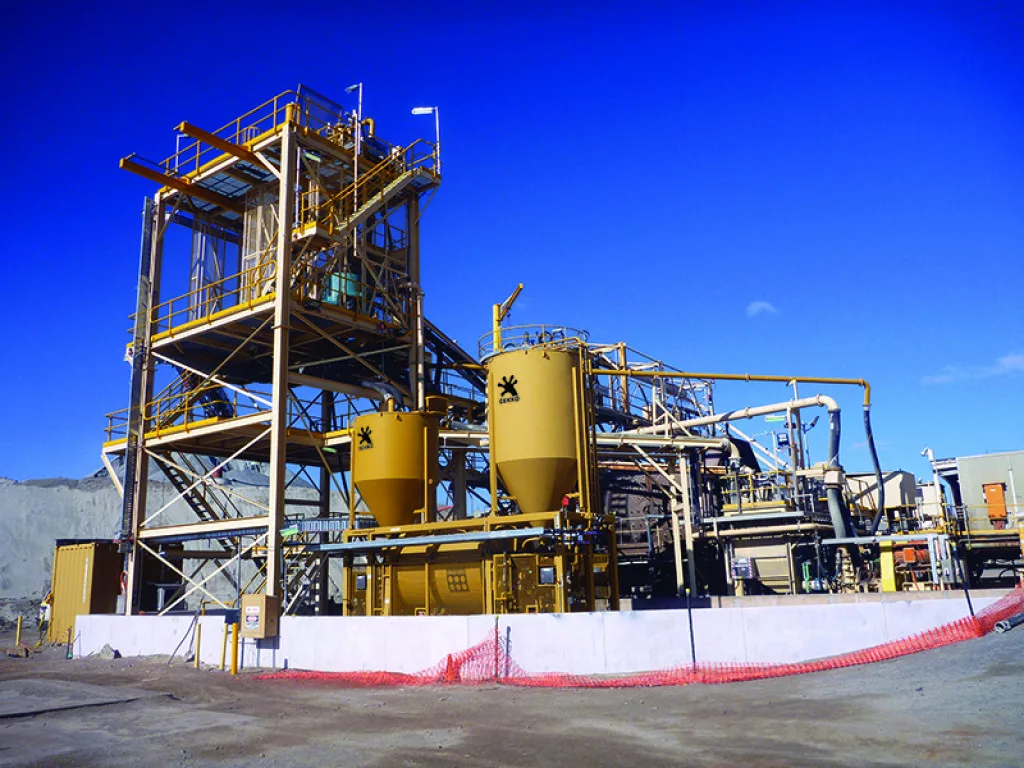
Plans for investment
As a result of the cyclical nature of the mining business, Gekko has made a large technological investment in an alternative energy initiative called Gaia EnviroTech (Gaia). A sister company to Gekko, Gaia is all about using previously gained engineering know-how and modular systems experience in developing Anaerobic Digestion (AD) systems and composting technologies.
“The development of this waste-to-energy system is in line with our fundamental goal of reducing energy from our mineral processing systems,” Grigg explains.
Coming out of the COVID-19 pandemic, it was important for Gekko to maintain its market presence within the gold industry and continue to ensure that its key capital equipment was being utilised in the new gold plants being built. Due to the high price of gold, the company has achieved this with multiple ILR sales made over the last 12 months. Gekko was able to supply over 15 units worldwide in the past year, marking a fantastic effort from the company collectively.
Moving forward, Gekko is directing its focus towards increasing its service offerings, getting back to travelling, visiting its global partners and improving the overall customer service.
“We are extremely focused on getting our newer products like the Carbon Scout and the OnLine Gold Analyser (OLGA) fully developed and out into the market over the course of the next year,” finishes Grigg.
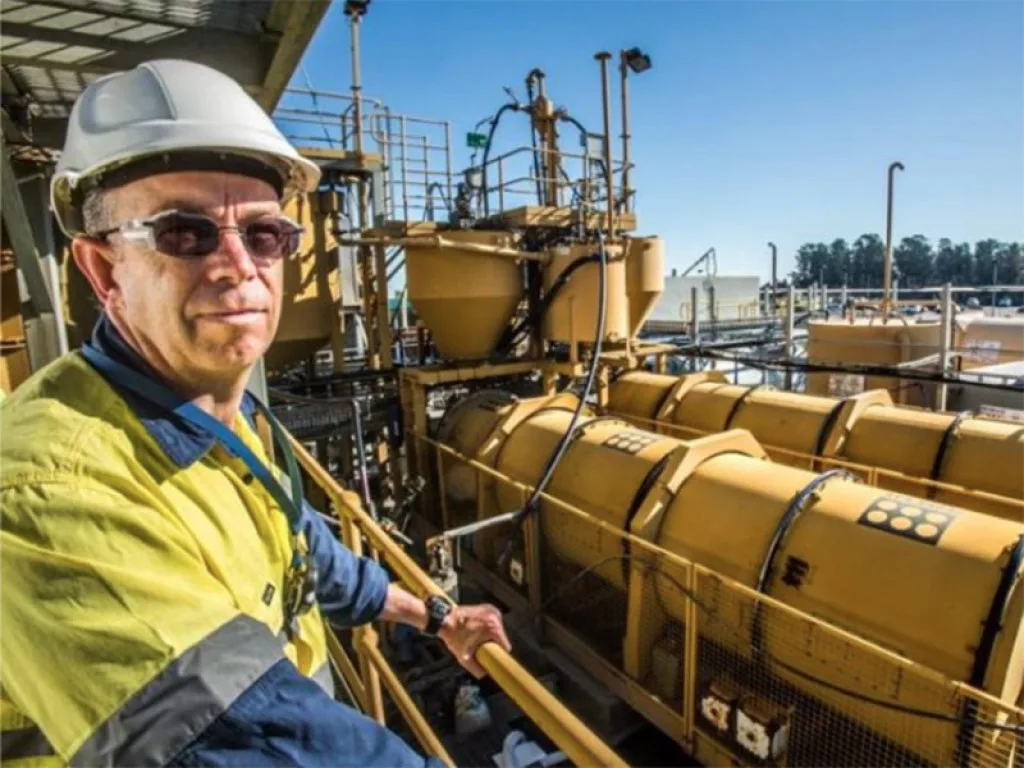
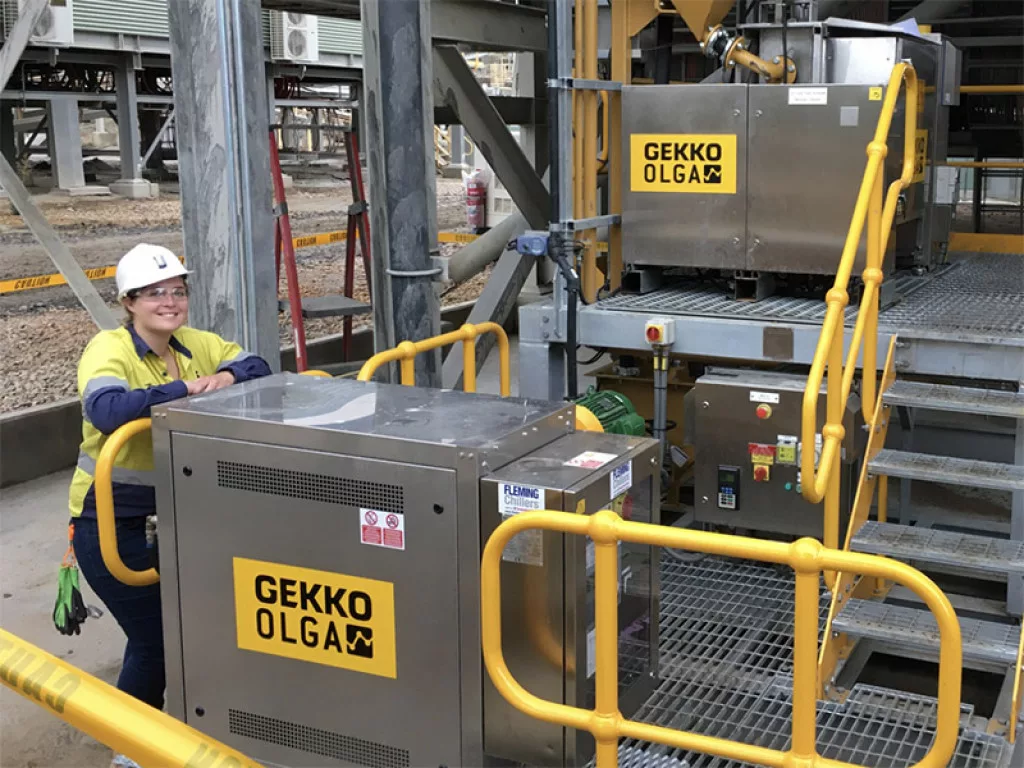
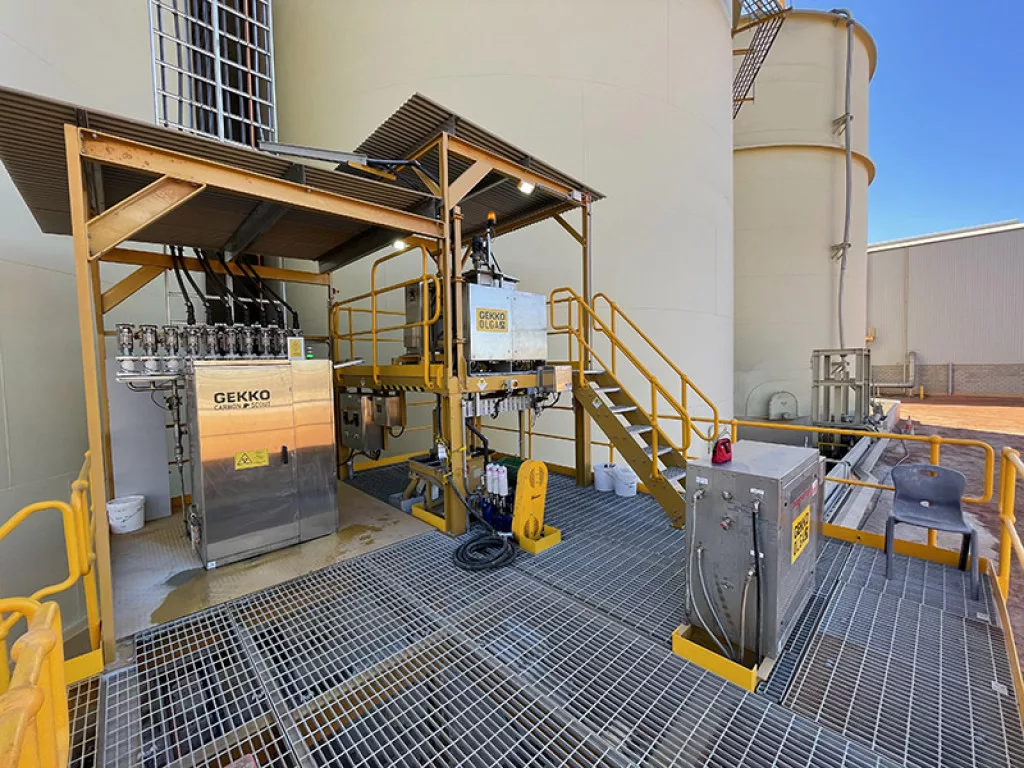