Ausdrill’s leadership team come together to discuss its extensive presence in the Australian drilling and blasting scene, growing ability to provide innovative technological solutions to increase mine site safety and efficiency, and aspirations for the future.
WE KNOW THE DRILL
Since its establishment in 1987, Ausdrill has provided safe, reliable, and productive drilling and blasting services across Australia.
Now part of the Perenti’s Drilling Services division, the company works with a range of clients, from major mining houses to junior explorers and developers, all of whom require high levels of efficiency and quality on their mining projects.
Ausdrill’s vast resource exploration, development, and production drill suite includes diamond core, reverse circulation, and grade control.
“We have designed and manufactured in-house a specialised lake drill for exploration drilling, whilst our industry-leading Rock Commander provides a bespoke solution to drilling around underground workings,” introduces Matt Clinch, Business Development and Improvement Manager.
Due to its considerable reach and flexibility, the Rock Commander 330 is especially useful in pits with historical underground workings, providing a highly safe and efficient drilling method in and around voids.
With a range of drilling units at its disposal, achieving hole sizes from as small as 76 millimetres (mm) and up to 311mm, the company’s diversity is unparalleled.
“We have explosives delivery mobile processing units (MPUs) capable of suitably loading both large and small-diameter blast holes,” Clinch adds.
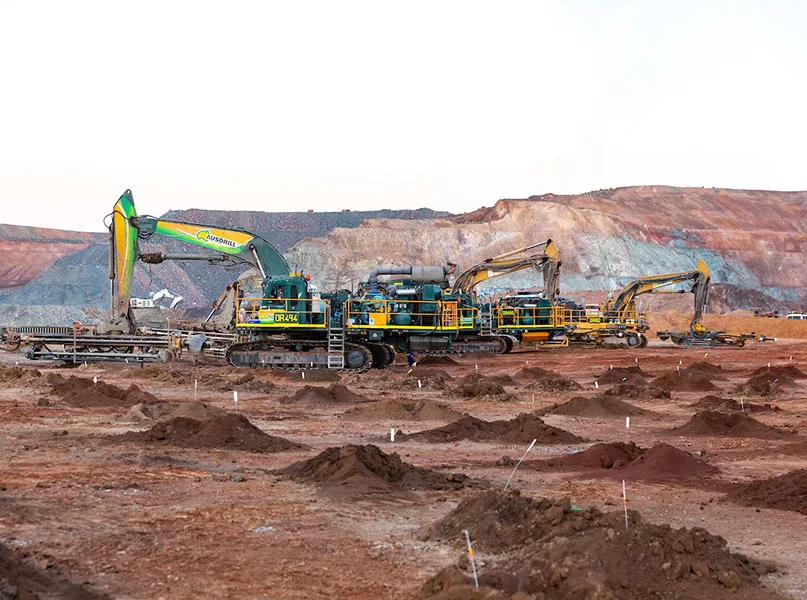
Another operational focus for Ausdrill is geotechnical services and understanding its client’s risks, particularly when it comes to loose or unstable rocks. As such, Ausdrill’s geotechnical services include rope access meshing and wall scaling capabilities which utilise trained professionals to mitigate the risks posed by wall instability.
To further improve the efficiency and safety of traditional rock scaling, Ausdrill partnered with the University of Technology Sydney (UTS) and the Innovative Manufacturing Cooperative Research Centre (IMCRC) to create the rock-scaling robotic system, High Access Localised Operations (HALO).
The two-year project introduced robotic and virtual reality (VR) technologies to relocate rope access technicians to a safe distance and remote control a robot based on data transmitted via video and Light Detection and Ranging (LiDAR) technology, allowing rope access technicians to work from a distance.
The robot can manoeuvre over the crest line to descend the wall, rattling and dislodging loose debris and potentially hazardous rocks.
As Ausdrill looks to further develop and improve HALO, it is also exploring the integration of remote VR digital twin technology elsewhere in its suite of mining rigs and services, demonstrating its constant commitment to ongoing innovation.
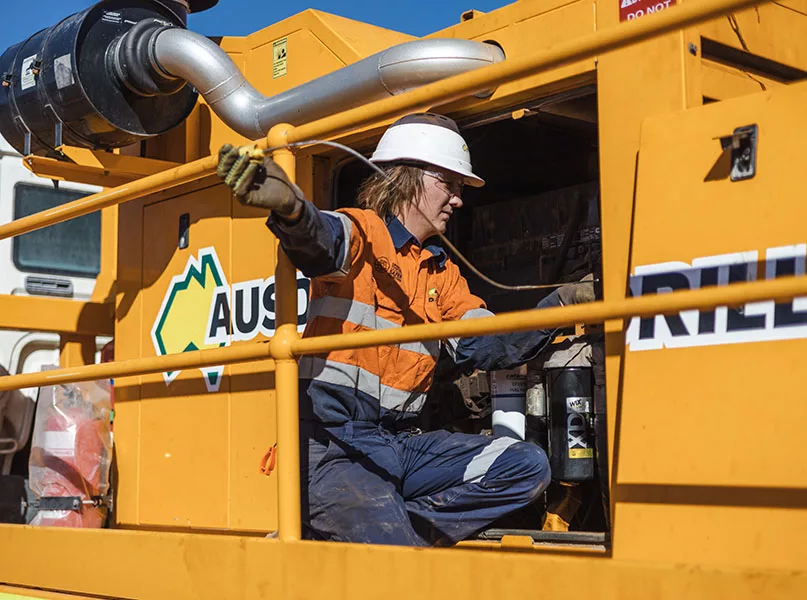
INNOVATING SAFETY
As an original equipment manufacturer (OEM) with over 37 years of experience in the mining sector, Ausdrill specialises in building customised drills for its clients’ unique projects.
“We are also dedicated to developing cutting-edge technology and continue to invest in projects such as one-touch drilling, remote drilling, hands-free technology, and our patented hands-free Auto Sampler,” reveals John Ivanovski, Senior Manager of Operations.
Ausdrill’s patented Auto Sampler is primarily used in grade control environments and continues to set new standards in safety performance, operational efficiency, and quality control.
The Auto Sampler utilises the RayTrac radio frequency identification (RFID) digital sample tracking system to ensure that every sample is tracked in sequence. The sample data is then uploaded to the client’s database.
Eliminating the need for human intervention, the Auto Sampler improves safety, ensures accuracy, and saves valuable time, labour, and on-site costs associated with sample collection on a drill rig.
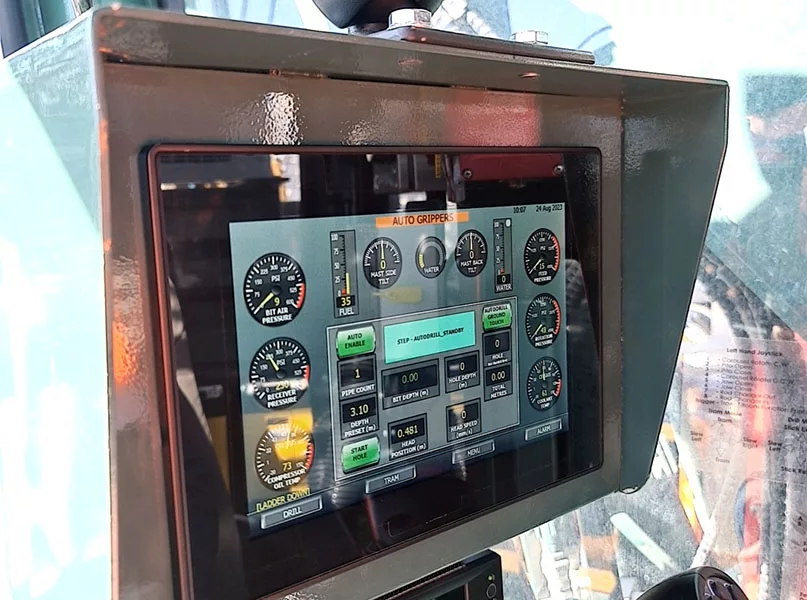
TRANSFORMING SAFE AND PRODUCTIVE MINING
Initially awarded to Ausdrill in 1989, the Kalgoorlie Consolidated Gold Mines (KCGM) Super Pit project is one of Australia’s largest open-pit gold mines.
Located approximately 600 kilometres (km) east of Perth, Western Australia (WA), the project currently employs around 115 Ausdrill workers.
It also operates 14 long-reach Rock Commander drill rigs, three grade control drills, and one reverse circulation (RC) drill, all of which are owned and maintained by Ausdrill’s in-house maintenance division.
“We are committed to having a locally based workforce and presence in Kalgoorlie with all key management residing locally on-site, supported by the Ausdrill Kalgoorlie branch,” Ivanovski details.
Congruent with the company’s commitment to supporting its workforce, the Rock Commander long-reach drills have transformed safe and productive mining at the KCGM Super Pit mine site.
“Originally designed to provide an effective approach to void management for KCGM operations, the Rock Commander long-reach drill keeps our employees at a safe distance from potential voids and away from high walls where rock falls may occur,” he elaborates.
This is due to the Rock Commander’s multi-echelon approach, which allows it to drill three lines without needing to tram. This reduces trip hazards for the blast crew by eliminating the need to turn tracked machines on the patterns.
In addition, the training cab Rock Commander, a two-seat operator training unit for hands-on experience, allows Ausdrill to improve the quality of training for its employees.
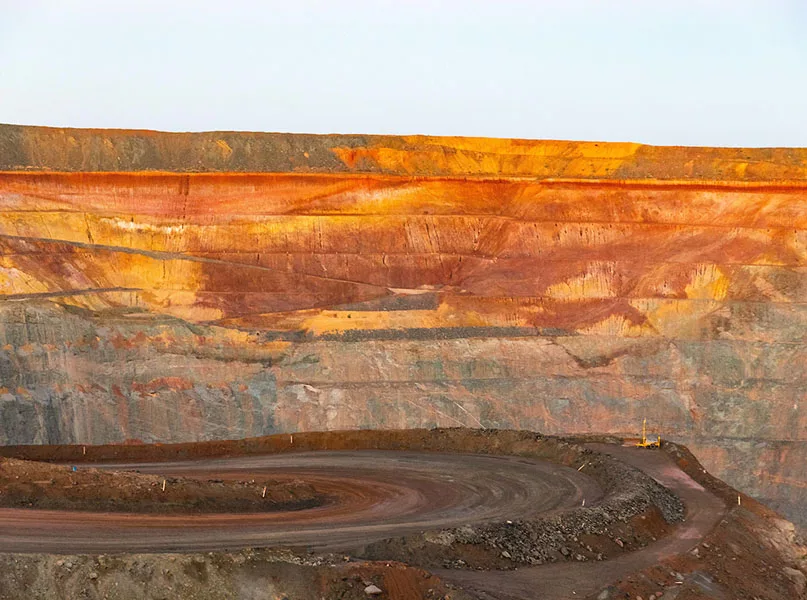
EXPERTISE AND ADAPATABILITY
Having operated at the St Ives Gold Mine on Lake Lefroy in Kambalda, WA, for more than 25 years, Ausdrill has worked hard to overcome challenges posed by the area’s harsh environment.
The lake itself is a huge salt pan with hazardous conditions, including deep mud beneath a salt crust.
“We have tackled these challenges by utilising tracked vehicles, designing custom-built drill rigs with extra-wide tracks, and even developing a hovercraft-mounted drill rig to access the most remote areas,” Ivanovski explains.
The company’s innovative approach has allowed it to successfully drill across the lake and surrounding lands with various methods.
“Our expertise and adaptability have been crucial in overcoming conditions that would be impossible for standard drilling equipment and solidified our reputation as a leader in surface mining,” he adds.
Specifically, Ausdrill has provided specialised multidirectional drilling capability to optimise hole trajectories, removing the guesswork to achieve targets, maximising resource extraction efficiency, and offering cost-effective solutions as safely and efficiently as possible.
The company’s activities on Lake Lefroy, enabled by its specialised lake drills, have consistently hit requisite targets, whilst its deep navigational diamond drilling capabilities have yielded significant cost savings at the St Ives gold mine site.
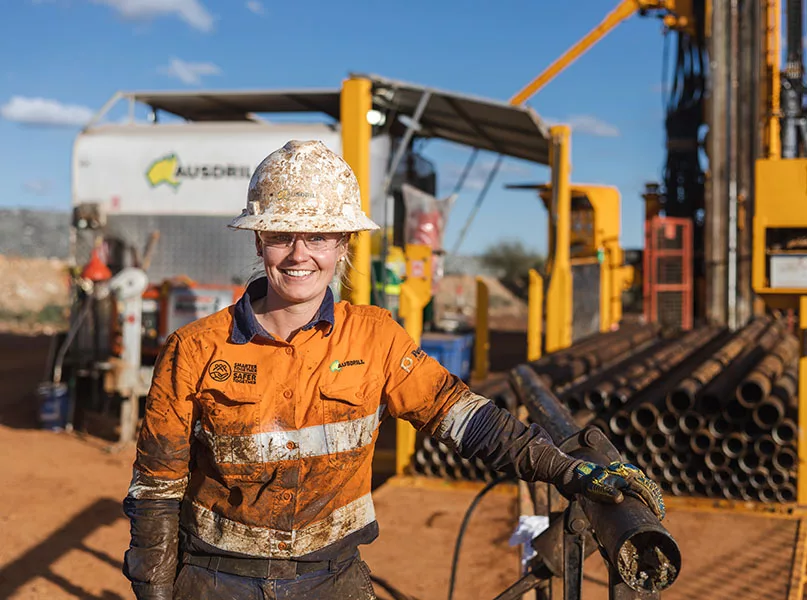
AUTOMATING DRILLING
Contributing to Ausdrill’s on-site safety, its semi-autonomous hands-free drilling equipment, which was used in BHP’s Nickel West project in Leinster, WA, has significantly reduced manual handling injuries.
“We’ve noticed a significant reduction in hand and back injuries while creating a safer and more inclusive environment for our diverse workforce,” Ivanovski observes.
The advanced technology can pre-select the required hole depth, drill down, and even change rods and flush the hole. As such, the need for manual, human intervention is not required, except for fine-tuning in the initial stages.
The recent introduction of hands-free Austex Engineering (Austex) rigs at the Nickel West project has raised the bar for Ausdrill’s operations, further enhancing the safety of its employees.
For example, the Austex X1550TH, a fully integrated electric over hydraulic diamond drill rig operated by a wireless remote, includes a cage barrier protecting the platform alongside human recognition cameras, which immobilise the drill’s function before technicians are able to access a live work area.
Furthermore, the drill rig’s remote monitoring system allows employees to access data points from anywhere across the world. This data is stored for internal analysis, enabling Ausdrill to further refine and optimise the drilling process for maximum productivity.
“Our investment in semi-autonomous, hands-free drilling equipment aligns with our key priority to reduce risk in our work environment and prevent life-changing events. The safety of our employees is our number one priority,” confirms Kym Low, General Manager.
With employee safety at the forefront of its drilling operations, Ausdrill sets a high bar across the industry.
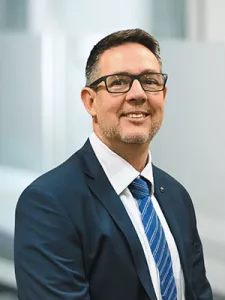
“Ausdrill’s partners are crucial to our success and enable us to deliver a valued service to our clients”
Matt Clinch, Business Development and Improvement Manager, Ausdrill
DELIVERING A VALUED SERVICE
Ausdrill’s supply chain is primarily managed in-house, with products sourced both locally and internationally.
“Ausdrill’s partners are crucial to our success and enable us to deliver a valued service to our clients. We have partnerships and relationships with major OEMs that consistently provide both reliability and leading technological solutions for our drilling service offerings to our clients,” Clinch outlines.
Ausdrill, part of Perenti Drilling Services (Perenti), is deeply involved in delivering the global mining services group’s purpose of creating enduring value and certainty, contributing to 4,726km of drill and blast and 2,621km of exploration drilling, according to the group’s 2024 annual report.
As part of Australia’s largest drilling contractor, Ausdrill continues to focus on innovation in safety, sustainability, and productivity as it provides clients with quality equipment and services.
“Our primary focus is to continue driving innovation in safety, sustainability, and productivity to deliver the highest quality equipment and services to our clients”
Kym Low, General Manager, Ausdrill
FUTURE REFLECTIONS
Looking ahead, Ausdrill will continue to expand its presence in Australia, where it was first established 37 years ago.
Its commitment to providing excellent drilling project management services with the highest safety standards across Australia hasn’t changed since its inception.
“Our primary focus is to continue driving innovation in safety, sustainability, and productivity to deliver the highest quality equipment and services to our clients,” Low divulges.
Dedicated to implementing cutting-edge technology and automation to mitigate manual handling risks and elevate the safety standards of its workforce, Ausdrill will continue to investigate innovative drilling technology.
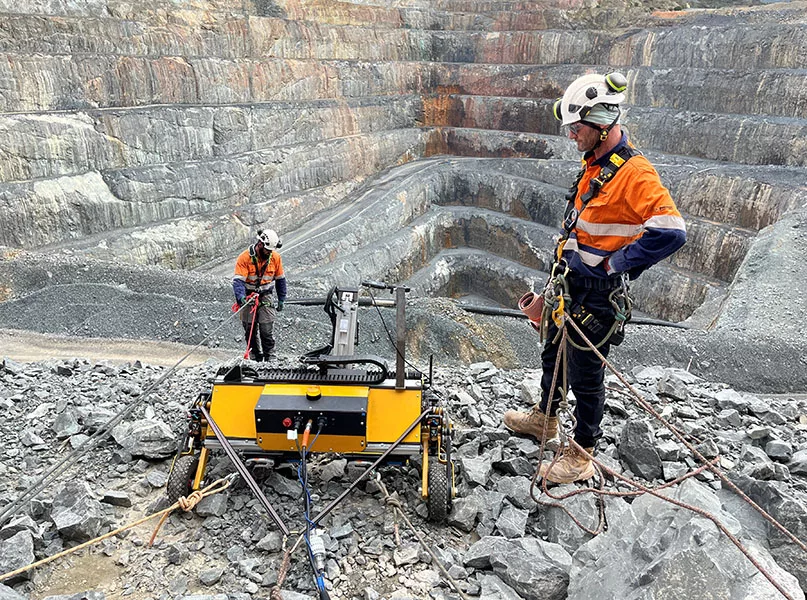
Furthermore, as much as its recruitment process is focused on achieving and maintaining Ausdrill’s trademark commitment to safety, it also concentrates on getting the right people for the job – which is rooted in diversity to obtain a range of skill sets and strengths.
This extends to fostering an environment where more women in the mining community can thrive and look forward to coming to work.
“With a progressive, 50:50 leadership team, Ausdrill is determined to create a safe, inclusive work environment, achieving greater gender balance in our organisation,” Low passionately concludes.
AUSDRILL PARTNER
