Tim Dobson, Managing Director, discusses how Magnetite Mines’ Razorback Iron Ore Project will help to enable low-emission green iron and steel production in Australia as the industry commits to decarbonisation.
THE KEY INGREDIENT FOR AUSTRALIA’S GREEN IRON TRANSITION
Magnetite Mines is an Australian Securities Exchange (ASX)-listed iron ore company focused on the development of magnetite iron ore resources in the highly prospective Braemar iron region of South Australia.
The company has a 100 percent owned mineral resource of six billion tonnes of iron ore and is developing the Razorback Iron Ore Project, located 240 kilometres (km) from Adelaide, to meet accelerating market demand for premium iron ore products created by iron and steel sector decarbonisation, with the potential to produce high-value direct reduction (DR)-grade concentrates.
The Razorback Project comprises two key deposits, namely Razorback and Iron Peak, which are part of the Braemar Iron Formation, a singular dipping tabular body with minimal structural complexity.
“The Braemar Iron Formation is a large geological formation that up until now has been undeveloped,” says Tim Dobson, Managing Director of Magnetite Mines.
“It’s not a new discovery; it’s been well-mapped, well-drilled, and is extremely well-delineated in terms of its mineralisation, so we know there’s a massive amount of magnetite available in this iron formation.”
The Razorback Project is somewhat different to other iron ore projects that have been developed globally over the years as it is able to produce extremely pure concentrate products required for green iron and steelmaking.
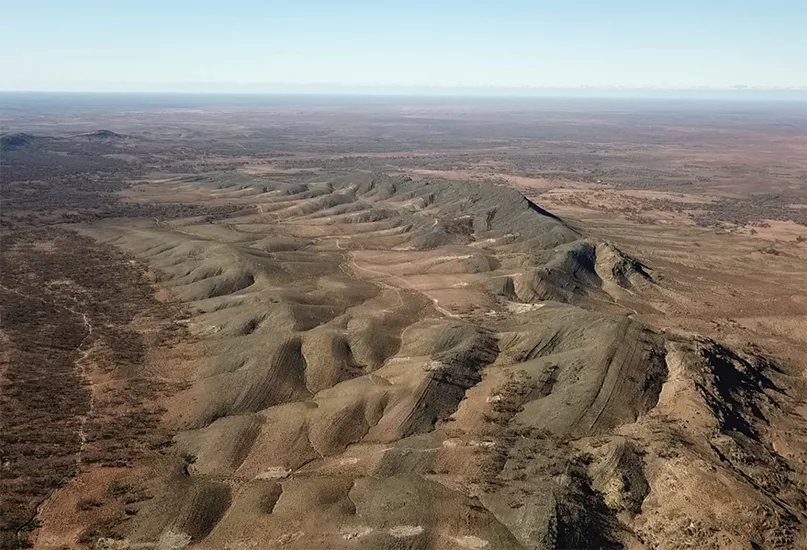
DECARBONISING STEEL
“The decarbonisation of the steel industry has made projects such as Razorback economically viable because of the premiums being commanded for high-grade concentrates,” Dobson insights.
Australia does not currently produce any iron ore or magnetite concentrate products that meet the very high-quality specifications required for the production of green iron, which is the key ingredient in green steel.
The Razorback Project can meet these specifications and is designed to deliver a long-term supply of magnetite concentrates to enable a new green iron production and export industry in the country.
“Even over the last 15 years, none of the magnetite projects developed in Australia are producing the high-grade products that are necessary for green iron production – this is what makes the Razorback Project stand out,” states Dobson.
As the global steel industry has committed to decarbonisation, the timing of Razorback’s development is in line with the forecasted increase in demand for the premium-quality iron ore products required to produce green iron.
Magnetite Mines has witnessed steelmakers increasingly shift towards decarbonising their operations, such as the move towards Electric Arc Furnace (EAF)-based steelmaking, but this transformation of the global steel industry will take time to play out.
“The decarbonisation of the steel industry has made projects such as Razorback economically viable because of the premiums being commanded for high-grade concentrates”
Tim Dobson, Managing Director, Magnetite Mines
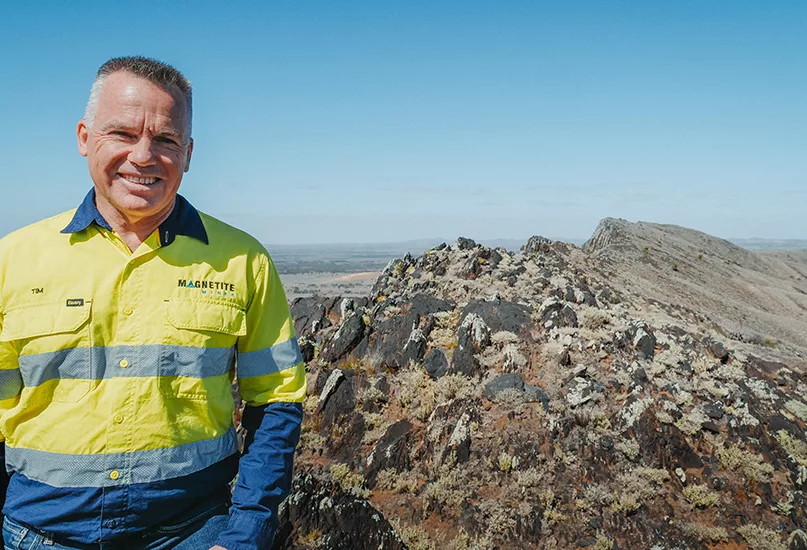
PURE PRODUCT
EAF-based steelmaking requires a very high grade of iron ore concentrate feeds. For this reason, the direct reduced iron (DRI) process, which removes oxygen from iron ore in solid form, i.e. without melting, cannot reject any impurities like blast furnaces can.
“What goes in comes out in the steel at the other end, so it has to be a very pure product,” Dobson emphasises.
Total global iron ore production that meets these specifications currently sits at about five percent, which aligns with annual DRI production levels.
“If you look at global steel production of almost two billion tonnes per annum, 70 percent comes out of blast furnaces and 25 percent comes from scrap being melted in EAFs or similar.
“That last five percent comes from DRI production, so it’s a technology that’s well known and was developed in places where there was no coal but lots of natural gas,” informs Dobson.
Traditionally, the concept of making green iron takes DRI technology and replaces natural gas with pure, green hydrogen molecules only produced from renewable energy.
Magnetite Mines’ Razorback Project aims to produce five million tonnes per annum of high-quality DRI feed grade concentrates, now considered a premium product, into a market that’s expected to grow as steelmakers implement EAFs and seek the supply chain to feed them.
The Razorback Project has the capacity to naturally expand to 10 million tonnes per annum, doubling the size of the operation.
“We’ll be able to expand our operations and production to match the increasing demand, so that’s a feature of our project configuration.”
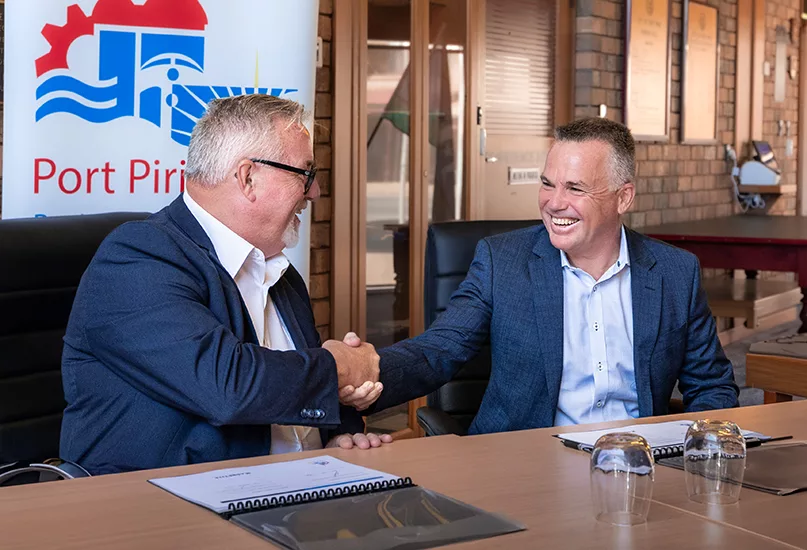
ALIGNMENT WITH GOVERNMENT
The Razorback Project is fully aligned with both the state and federal governments’ focus on creating a green iron industry, and South Australia is rapidly emerging as a strong candidate for future production.
“There are not many places in the world where renewable energy at scale and magnetite concentrates coexist, but South Australia is one of them,” Dobson tells us.
This year, the Government of South Australia commenced an Expression of Interest (EOI) process, seeking partners to jointly investigate the development of a green iron industry in the state by 2030.
“The government’s promise is that it will then align its policies and funding mechanisms to support that opportunity for the betterment of the state’s economic growth,” he adds.
The federal government has also recognised the opportunity and in May began consulting on opportunities to support the future growth of Australia’s green metals industry, a process that is aligned with the government’s flagship Future Made In Australia policy and associated fund.
The consultation aims to understand what the barriers are to decarbonising the production of green metals and what would encourage new investment, with the responses helping to guide policy development to support an Australian green metals industry.
Magnetite Mines has submitted its recommendations to the consultation for how the government should position its policies and support projects such as its Razorback Project.
In July, the company also signed a Heads of Agreement with JFE Shoji Australia Pty. Ltd. (JFE).
This landmark agreement with Japan’s second largest steelmaking group sets the framework for funding towards the Definitive Feasibility Study (DFS), the completion of which is central to progressing the Razorback Project to Final Investment Decision (FID).
Magnetite Mines believes that Razorback will be best developed via a joint venture (JV) with motivated investors and offtake partners,
“Razorback is the one and only project that JFE has decided to sign a Heads of Agreement with to support and fund its development and potentially become our first JV partner,” shares Dobson.
“We couldn’t be more excited with the alignment of all these elements of industry, international investment, and government.”
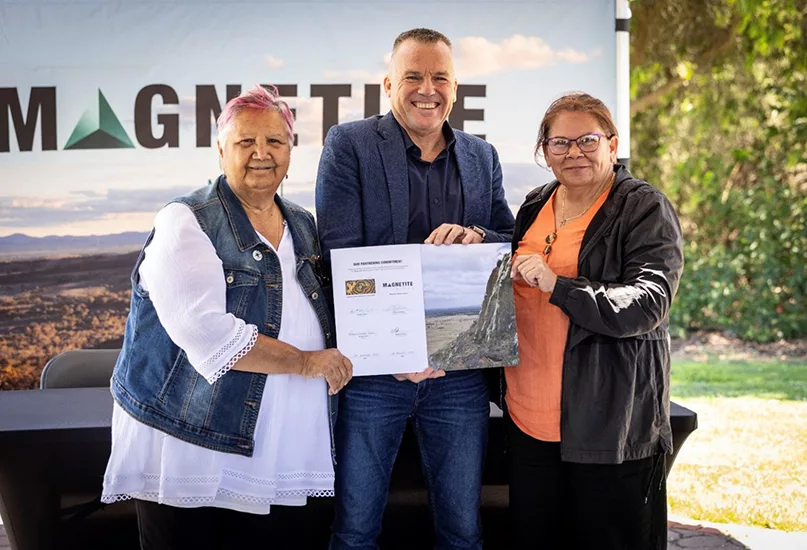
SUSTAINABILITY PIECE
Whilst Magnetite Mines is solely focused on Razorback, the company also takes its sustainability responsibilities and obligations extremely seriously.
Dobson himself is motivated to be a role model in terms of sustainability, particularly when it comes to stakeholder relations.
“We’ve spent two years building trusted, respectful relationships with the Traditional Owners, the Ngadjuri people, who have recognised native title over the land where our project is located, and formalised that relationship into a voluntary partnering agreement. That’s one example of how we’re taking our sustainability approach seriously,” he affirms.
The company has also signed two Memoranda of Understanding (MoUs) with local governments to work hand in hand with them on the socioeconomic impacts in their regions.
“We’ve done that on purpose so that we are collaborating from the get-go rather than coming in later and, as sometimes happens, causing confusion or conflict when mining companies leave things unchecked until it’s too late.”
Magnetite Mines takes its sustainability obligations so seriously that it has launched ‘foresight’, a bespoke platform for the company’s approach to socially and environmentally responsible project delivery.
The launch of foresight embodies the company’s commitment to measuring and reporting its sustainability progress against objective global metrics to shareholders and stakeholders.
“All our sustainability works are done under the foresight banner, and that will be our brand as we go forward,” Dobson concludes.